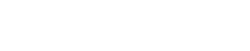
Nordberg® NP Seriesâ„¢ impact crushers are the solution when output and productivity demands are increasingly stringent, from quarry to industrial applications and from mining to recycling. It’s easy to build your own crusher configuration — by adding options for your application — like a full hydraulic breaker plate adjustment setting, a third breaker plate or feed chute and belt guard. The Self Rotor Rotation system (SRR) is available across the NP range and is part of Metso’s ongoing effort to innovate and find ways to enhance the quality, ease of use, and safety of its products. New NP automation (IC2000) controls the crusher operation and gives a perfect and complete overview of performance.
The different grades of steel and cast iron for the blow bars with the possibility for ceramic inserts make the NP Series impact crushers effective in numerous applications regardless to the material abrasiveness.
NP Series impact crushers feature a unique blow-bar attachment system. Combined with perfect blow-bar alignment on the crossbeam contact faces, this reduces risks of breakage and makes it possible to push the use of cast iron for blow bars beyond conventional limits. The rotor with high inertia improves crushing reduction and provides stability in the process, reducing energy consumption and increasing long-term performance.
Metso’s focus on customer success is clearly demonstrated in the product development of the NP Series impact crushers. We have been building impact crushers for 60 years, so we know that customers are looking for high performance to boost profitability. By combining the best technical solutions, our crushers provide a reliability that lets customers focus on their own operations.
Continuous collaboration with research laboratories results in state-of-the-art technical innovations in terms of durability of wear parts and reliability of mechanical components. Higher reduction with fewer crushing stages lowers your capital costs and saves energy. Mechanical reliability, and simplified process, easy machine operation, and easy and safe maintenance increase the global availability of the plant and profitability.
Nordberg® NP15™ offers a steeper feed angle to increase material penetration and make the discharge curve less sensitive to blow bar wear and therefore more consistent over time. This innovative design is usefull especially for HSIs in secondary and tertiary applications.
Metso innovates on NP15 with the new two part rear frame. The extra large opening of the new frame gives greater access to the breaker plates during wear part replacement. Metso developed a new breaker plate cassette design. This patented innovation consists of a removable assembly that allows changing the breaker plate liners in a safe condition, out of the crusher. The new maintenance bridge gives safe access to the rotor while changing blow bars, and also safe access to the highest side liners.
Feed opening | Maximum feed size | Maximum installed power | |
---|---|---|---|
NP1313 | 1 320 x 1 225 mm (52″ x 48″ 1/4) | 900 mm (35″) | 250 kW (350 hp) |
NP1415 | 1 540 x 1 320 mm (60 5/8″ x 52″) | 1 000 mm (40″) | 315 kW (400 hp) |
NP1620 | 2 040 x 1 634 mm (80 1/4″ x 64 1/4″) | 1 300 mm (51″) | 500 kW (700 hp) |
NP2023 | 2 310 x 1 986 mm (91″ x 78 1/4″) | 1 500 mm (59″) | 1 200 kW (1 600 hp) |
NP1110 | 1 020 x 820 mm (40 1/4″ x 32 1/4″) | 600 mm (24″) | 200 kW (250 hp) |
NP1520 | 2 040 x 995 mm (80 1/4″ x 39 1/4″) | 700 mm (28″) | 500 kW (700 hp) |
NP13 | 1 320 x 560 mm (52″ x 22″) | 350 mm (14″) | 315 kW (400 hp) |
NP15 | 1 540 x 600 mm (60 5/8″ x 24″) | 400 mm (16″) | 355 kW (450 hp) |
Nors Construction Equipment Canada GW, Ltd193 RailPark Way, R4B 0A8
Nors Construction Equipment Canada GW, Ltd10 Lindeman Road Y1A 5Z6
Nors Construction Equipment Canada GW, Ltd 2011-14th Ave,
V9W 4J2
Nors Construction Equipment Canada GW, Ltd 2401 Cranbrook Street North V1C 3T3
Nors Construction Equipment Canada GW, Ltd 12623 Charlie Lake Frontage Road V1J 2B0
NorsConstruction Equipment Canada GW, Ltd 1220 Chief Louis Way V2H 1J8
Nors Construction Equipment Canada GW, Ltd 2115 South Wellington Road V9X 1R5
Nors Construction Equipment Canada GW, Ltd 7411 Riggs Crescent V2N 0H1
Nors Construction Equipment Canada GW, Ltd 3830 Sharples Road V8G 5P8
NorsConstruction Equipment Canada GW, Ltd 18995 - 94th Ave Surrey, BC V4N 4X5
Nors Construction Equipment Canada GW, Ltd 123 L & A Cross Road Spallumcheen, BC V1B 3S1
Nors Construction Equipment Canada GW, Ltd 4700 Collier Place V2G 5E9
NorsConstruction Equipment Canada ST LP 25616 117 Avenue T7X 6C2
Nors Construction Equipment Canada ST LP 7923 – 54 Street S.E T2C 4R7
Nors Construction Equipment Canada ST LP 310 MacKenzie Boulevard T9H 4C4
NorsConstruction Equipment Canada ST LP 11301 – 89th Avenue T8V 7M9
Nors Construction Equipment Canada ST LP 6 Burnt Lake Crescent T4S 2L4