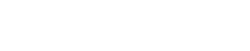
It’s well known in the construction industry knows that a wide range of heavy equipment is at the heart of every contractor’s operation.Â
As a contractor, you heavily depend on your equipment to get you through every project. It is of utmost importance you know exactly how your equipment is functioning at all times, so you can ensure that you are maximizing its use and are aware of any causes for concern before they escalate into unmanageable problems.Â
Telematics software systems log and report relevant data on your construction equipment. They do that using GPS technology and onboard diagnostics and monitoring sensors. Then, that data is generally assessed through a web portal and translated into valuable insights into your equipment’s location, fuel consumption, idle times, machine alerts, etc.
Telematics software systems are typically compatible with any kind of computer. They can also be accessed from any mobile device connected to the web. Therefore, not only do telematics systems provide important data sets related to your machinery, but they also make it extremely convenient to access and analyze that information.
Whether it is to manage equipment better, increase profitability, or optimize the finer details of your day-to-day work, there are many fantastic reasons to integrate telematics into your contracting operation. The following are some of the most significant ways that you can gain from this brilliant software:
If you have multiple machines used on one or more job sites, you will probably want to see exactly how each machine is used. Telematics can certainly help with that since it will provide you with data to show whether you may be allocating too much equipment or not enough equipment to a specific site. This data will also show exactly how much each machine is being used in its current location.
Rather than leaving valuable equipment on a site where it is not needed, you could be reallocating it to somewhere where it is. If you lack equipment in another location, resulting in the overuse of the equipment, it could cause problems. Addressing asset allocation needs is up to you, but telematics will make it easier to reveal what those needs may be.Â
Dealing with the maintenance and repairs of your equipment can be one of the most frustrating parts of being a contractor, especially when that kind of thing comes up unexpectedly. However, telematics can make a huge difference by limiting the unexpected downtime on your machinery by keeping you updated constantly on the current state of everything you have.Â
Telematics can also help you track how many working hours each of your machines has racked up, so you never have to worry about taking something in for its regular maintenance too early or too late.Â
If a fault code comes up on a piece of your equipment, or one of your machines seems to be performing more poorly than usual, these could also be signs some maintenance is required. Fortunately, with a good telematics system, you will be aware of either of these issues immediately, so you can take action before the situation worsens.Â
By identifying these problems early, you will ultimately extend the life of your equipment and save on your repair and labour costs.Â
Knowing the operating costs for each piece of equipment in your fleet is rather important, especially if the operational costs of any of them begin to exceed ownership costs. These costs, related to fuel consumption, preventative maintenance, operator wages, repairs, and tire/track costs, can all give you a pretty good indication of a machine’s life cycle.Â
Fortunately, with a telematics system in place, you can track all of that relevant data easily. Of course, if there are areas where operating costs can be reduced, such as cutting down on idling time or correcting operator behaviour, your telematics data will reveal that, too, allowing you to manage such things as you see fit.Â
In addition to the significant savings that could come from managing your operating expenses more efficiently, there are numerous other ways to employ telematics software to save you money. Did you know that the government collects excise taxes on gasoline and diesel? It’s true, and these taxes are generally used to help fund road construction or highway maintenance projects.Â
However, when businesses use fuel for off-road purposes, like construction equipment, they usually get a tax refund, but only if they can produce records of how much fuel they used off-road. Thanks to the GPS tracking and fuel consumption tracking that telematics software has, that is much easier.Â
Additionally, it is common for some insurance providers to reduce or eliminate deductibles or offer discounts if your equipment has GPS tracking paired with geo-fencing alert capabilities, which telematics will take care of.Â
That can amount to a significant amount of savings when it comes to insuring your fleet. Telematics will also allow you to keep your job sites safer, meaning fewer accidents and even further savings on insurance costs.Â
Nors Equipment can help you set up heavy equipment monitoring British Columbia for your fleet. In doing so, you can benefit from all the above advantages, making your operation increasingly efficient, streamlined, and cost-effective. Our telematics system, called Volvo ActiveCare Direct (ACD), will allow you to monitor your equipment in real time, alerting you whenever action is needed.Â
With ACD, you don’t have to sort through alarms and error codes after receiving your telematics data. Volvo analyzes that data for you. It prioritizes case reports that need immediate attention, making everything more direct and efficient, which is one of the main reasons ACD leads the telematics industry. ACD also provides details about issues, potential causes, and suggested actions via email.Â
ACD has been proven to save businesses a significant amount of money, and we can help your business achieve such savings. Most of our customers using ACD have reduced their fuel costs by 10-15%, idle times by about 7%, and increased overall machine utilization by 5-10%. Savings on costly equipment repairs are commonly reduced as machine misuse problems decrease.Â
For more information about the advantages of using our ACD telematics system or to request a tutorial from one of our dedicated telematics specialists, call Nors Equipment at 1-833-730-0613 or contact us here.
Nors Construction Equipment Canada GW, Ltd193 RailPark Way, R4B 0A8
Nors Construction Equipment Canada GW, Ltd10 Lindeman Road Y1A 5Z6
Nors Construction Equipment Canada GW, Ltd 2011-14th Ave,
V9W 4J2
Nors Construction Equipment Canada GW, Ltd 2401 Cranbrook Street North V1C 3T3
Nors Construction Equipment Canada GW, Ltd 12623 Charlie Lake Frontage Road V1J 2B0
NorsConstruction Equipment Canada GW, Ltd 1220 Chief Louis Way V2H 1J8
Nors Construction Equipment Canada GW, Ltd 2115 South Wellington Road V9X 1R5
Nors Construction Equipment Canada GW, Ltd 7411 Riggs Crescent V2N 0H1
Nors Construction Equipment Canada GW, Ltd 3830 Sharples Road V8G 5P8
NorsConstruction Equipment Canada GW, Ltd 18995 - 94th Ave Surrey, BC V4N 4X5
Nors Construction Equipment Canada GW, Ltd 123 L & A Cross Road Spallumcheen, BC V1B 3S1
Nors Construction Equipment Canada GW, Ltd 4700 Collier Place V2G 5E9
NorsConstruction Equipment Canada ST LP 25616 117 Avenue T7X 6C2
Nors Construction Equipment Canada ST LP 7923 – 54 Street S.E T2C 4R7
Nors Construction Equipment Canada ST LP 310 MacKenzie Boulevard T9H 4C4
NorsConstruction Equipment Canada ST LP 11301 – 89th Avenue T8V 7M9
Nors Construction Equipment Canada ST LP 6 Burnt Lake Crescent T4S 2L4