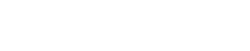
Hydraulic breakers mounted on excavators are ideal for breaking rocks, asphalt, concrete, as well as other construction and aggregate materials. Nevertheless, if you want your attachment to last for a long time, you will need to keep routine maintenance top of mind.
If you do not perform routine maintenance on your attachment, you are more likely to derail your project, costing you time, money, and possibly decreasing the lifespan of the attachment. Follow these six tips and you will be able to achieve optimal performance and longevity from your heavy-duty hydraulic breaker.
Although inspecting a hydraulic breaker for wear and tear is a relatively straightforward process that doesn’t take long at all, many operators overlook it. To help identify worn or damaged items, a visual inspection needs to be carried out before each time the breakers are used. This will help prevent unexpected downtimes that could occur.
Visual checks should be performed regularly so those items that are beginning to wear can be spotted early, which can help prevent failures down the road. Make sure that all hydraulic hoses are intact, along with the breaker shell, the attachment pins, the tool retainers and locks, and any cracks or dents on the tool point.
The lower bushing of many breakers, the top angle of the tool, and the retaining pins can all be measured with a specialized check tool provided by the manufacturer. By using this maintenance tool for the authorized checks of its recommended parts, the chances of an early failure of the components will be reduced.
To use the maintenance tool properly, the first thing you need to do is remove the retainer pins and breakers tool. Seeing as how you have just removed the breaker tool, this may be a good time to give it a good inspection for cracks and to use the maintenance tool in checking the top angle. Furthermore, look for wear and damage on the retainer pins as well.
The bushing on the breaker should be checked next. When inserting the maintenance tool into the bushing, the tool must fit end-to-end inside the bushing. If it cannot, then the bushing must be replaced. It takes no more than 15 minutes to run this simple check and should be conducted at least once a week or every 50 hours that you use the attachment.
It is important to pay attention to wear on the bushing, as this can adversely affect tool performance. As a result of bushing wear, the breaker tool will have front-to-back play that can cause piston misalignment.
For a reduced amount of wear and possible downtime, hydraulic hoses from the excavator should be routed properly and be of the correct length. Extending attachments with hoses that are too short can limit their range of motion. On the other hand, it is important to remember hoses that are longer in length may catch on rebars and other debris and become disengaged. To maximize operating time and protect hydraulic hoses, look for hydraulic hoses that are standard lengths for each of your machines.
Lubricating the hydraulic breaker and clearing the tool bushing area of debris is the most important maintenance task. In order to prevent metal-on-metal contact, it is recommended to use a No. 2 lithium-based grease with 3 percent moly grease heated to 500 degrees Fahrenheit. With a grease type such as this, the steel and bushings remain lubricated longer at higher temperatures than with ordinary lubricants.
There are two types of greasing methods you can choose from: manual greasing and automatic greasing. To reduce buildup, tool wear, and bushing wear, if you are using a hydraulic breaker that needs to be manually greased, then make sure to do so following manufacturer recommendations—typically, every one to two hours.
Hydraulic breaker models from some manufacturers come with an automatic lubrication (greasing) system that provides an unbroken flow of grease instead of having to manually grease the machine. Lubrication can either be mounted directly on the breaker cradle or in a larger tank mounted on the machine. By using an automatic hydraulic breaker, you are able to save yourself labour-intensive time, money down the line, and the risk of over-greasing the hydraulic breaker.
Tool points should be matched to their respective applications in order to maximize jobsite production and extend breaker lifespans. It is common for hydraulic breakers to be equipped with four different points—the most common being the moil tool point. Standard features include a set of moil points that can be used for everyday demolition tasks.
These are some of the other tool points:
The nitrogen charge pressure should be calculated according to the application as well as the temperature outside.
If one is breaking rocks, then the nitrogen level should be different from when one is breaking concrete in a parking lot. Outside temperatures are also a factor. You can find the nitrogen pressure settings in the attachment’s Operations and Maintenance Manual based on your application and working temperature.
The fact that breaker attachments are not universal across all carriers is also an important point to note. For material to break effectively, each breaker must be properly sized for the carrier it is intended to be used on. If a breaker is too large for the carrier, for example, then energy is displaced, which can also decrease the impact of the breaker on the material.
Too small of a breaker can cause excessive pressure on the working steel and other mounting components, possibly damaging them. You should work with your heavy equipment dealership to make sure the breaker will be compatible with the carrier’s weight, hydraulic oil flow, and pressure, and will fit the application for which the breaker will be used.
By following the above tips, you can help extend the life of your heavy construction attachments while increasing their use on multiple job sites. To learn more, call Nors Equipment at 1-888-492-4365 or contact us with any questions.
Nors Construction Equipment Canada GW, Ltd193 RailPark Way, R4B 0A8
Nors Construction Equipment Canada GW, Ltd10 Lindeman Road Y1A 5Z6
Nors Construction Equipment Canada GW, Ltd 2011-14th Ave,
V9W 4J2
Nors Construction Equipment Canada GW, Ltd 2401 Cranbrook Street North V1C 3T3
Nors Construction Equipment Canada GW, Ltd 12623 Charlie Lake Frontage Road V1J 2B0
NorsConstruction Equipment Canada GW, Ltd 1220 Chief Louis Way V2H 1J8
Nors Construction Equipment Canada GW, Ltd 2115 South Wellington Road V9X 1R5
Nors Construction Equipment Canada GW, Ltd 7411 Riggs Crescent V2N 0H1
Nors Construction Equipment Canada GW, Ltd 3830 Sharples Road V8G 5P8
NorsConstruction Equipment Canada GW, Ltd 18995 - 94th Ave Surrey, BC V4N 4X5
Nors Construction Equipment Canada GW, Ltd 123 L & A Cross Road Spallumcheen, BC V1B 3S1
Nors Construction Equipment Canada GW, Ltd 4700 Collier Place V2G 5E9
NorsConstruction Equipment Canada ST LP 25616 117 Avenue T7X 6C2
Nors Construction Equipment Canada ST LP 7923 – 54 Street S.E T2C 4R7
Nors Construction Equipment Canada ST LP 310 MacKenzie Boulevard T9H 4C4
NorsConstruction Equipment Canada ST LP 11301 – 89th Avenue T8V 7M9
Nors Construction Equipment Canada ST LP 6 Burnt Lake Crescent T4S 2L4