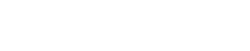
Over the last decade, telecommunications technology has made enormous advances. It can speed up the process and make the job safer for construction companies.
However, last year marked the biggest shift. Through COVID-19, the technology proved to be the hero by reducing travel to construction job sites, keeping job schedules on track, and increasing safety on construction sites.
For years now, telematics has been used by the construction industry to drive change. Companies need even more than they did just a few years ago to stay competitive and profitable – greater connectivity, greater upgrades, and deeper data insights.
While the technology for data analysis continues to advance, telematics is becoming more commonly used. In recent years, telematics has become more popular for large, mid-size and small equipment. With aftermarket options now available, leading to drastic price reductions for basic information, many smaller equipment types, like generators, are being added to fleet telematics reports.
Telematics extends the capabilities of your fleet by allowing real-time monitoring and critical decisions to be made in minutes as opposed to hours or days. When your equipment malfunctions, site managers and equipment dealers are alerted right away, and can dispatch technicians to fix the equipment with the appropriate parts, avoiding costly diagnostic and travel time.
In large sites with multiple machines, telematics data can provide a big-picture picture of the equipment’s health. Data collected and analyzed can be filtered and compared against historical records to improve efficiency and design preventive maintenance programs and operator training programs.
These programs can track job progress in real time, understand how operators use equipment, notify maintenance personnel in advance of service intervals so these can be scheduled when the equipment is not in use, allow for remote diagnostics and track the locations of all of your assets . We’ve all known somebody who has had a piece of equipment walk off the job! Most telematics options will include the ability to set alarms or notifications if your equipment is leaving a specified area or is turned on during designated down time between shifts.
When used properly, telematics can have a significant impact on business costs. Using it can help plan maintenance, bid on upcoming work, reduce operator abuse and increase productivity and efficiency on any job site. Telematics is already installed in next-generation machines, allowing more operators to use the technology. Increasing productivity, operator training, and preventive maintenance follow next.
Construction firms are increasingly using data-driven analytics to plan and manage their operations. In addition, remote access enables site managers to keep tabs on data without ever leaving their office.
Companies now capture a significant amount of data related to equipment operations to gain a deeper understanding of these operations. This can also pose a challenge on larger construction sites with upwards of 10,000 items of connected equipment. Getting the best out of this information creates a new challenge.
To succeed in your operation, you must understand the critical information. Avoid metrics that are irrelevant to your business. GPS tracking and daily reports are often the only requirements. Several users require a full dashboard that can display historical information on equipment, track its location, indicate idle time or identify fault codes to aid in remote troubleshooting.
Telematics could predict future behaviour and identify problems before they arise. Using telematics, the operator can immediately contact the technical support team if they are experiencing trouble with their equipment. In addition to logging in to the machine, the dealer can also access live machine diagnostic information to identify any problems. A technician can be dispatched to fix the machine using the right parts and tools whenever a repair is needed, saving money and time.
The use of telematics for payload systems can provide information on fuel consumption, cycle times and volume moved. Construction firms can then use these metrics to estimate cost per ton, allowing them to control productivity and price their jobs better.
Telematics is becoming a more important tool for tracking greenhouse gas emissions from equipment. Technology has become a critical piece of a construction company’s sustainable efforts to significantly reduce fuel consumption, emissions, and carbon footprint.
Real-time reporting can help address operator behaviour, such as excessive speeding, idling, and braking suddenly, leading to high fuel consumption and CO2 emissions.
In addition to providing insight into route selection for optimal fuel consumption, telematics systems can also be employed to improve dispatch times by scheduling technicians closest to jobs and monitoring machine uptime and maintenance to ensure optimal performance. As a method of showing environmental progress and proving compliance, sustainability data can also be included on invoices.
On a global and local scale, sustainability in construction is a major concern for governments and corporations alike. The immediate future will see addressing and lowering emissions in the construction industry becoming a regulatory requirement.
In addition to assisting green initiatives and emissions reduction goals, carbon footprint analysis will help maximize equipment energy efficiency.
COVID-19 has unknowingly led to greater use of telematics, which will have lasting effects on the industry long after the pandemic is over. As telematics evolves, the industry will see greater advancements, such as increased efficiency and productivity, resulting from long-term benefits and connections.
To ensure the continued growth of the construction industry, telematics must be integrated into a wider strategy. The first step is to believe that telematics can significantly improve and transform your business. It can lead to efficiencies, greater sustainability and competitiveness, and increase your bottom line by optimizing job sites.
To find out more about the care track by contacting Nors Equipment today, call us at 1-888-492-4365.
Nors Construction Equipment Canada GW, Ltd193 RailPark Way, R4B 0A8
Nors Construction Equipment Canada GW, Ltd10 Lindeman Road Y1A 5Z6
Nors Construction Equipment Canada GW, Ltd 2011-14th Ave,
V9W 4J2
Nors Construction Equipment Canada GW, Ltd 2401 Cranbrook Street North V1C 3T3
Nors Construction Equipment Canada GW, Ltd 12623 Charlie Lake Frontage Road V1J 2B0
NorsConstruction Equipment Canada GW, Ltd 1220 Chief Louis Way V2H 1J8
Nors Construction Equipment Canada GW, Ltd 2115 South Wellington Road V9X 1R5
Nors Construction Equipment Canada GW, Ltd 7411 Riggs Crescent V2N 0H1
Nors Construction Equipment Canada GW, Ltd 3830 Sharples Road V8G 5P8
NorsConstruction Equipment Canada GW, Ltd 18995 - 94th Ave Surrey, BC V4N 4X5
Nors Construction Equipment Canada GW, Ltd 123 L & A Cross Road Spallumcheen, BC V1B 3S1
Nors Construction Equipment Canada GW, Ltd 4700 Collier Place V2G 5E9
NorsConstruction Equipment Canada ST LP 25616 117 Avenue T7X 6C2
Nors Construction Equipment Canada ST LP 7923 – 54 Street S.E T2C 4R7
Nors Construction Equipment Canada ST LP 310 MacKenzie Boulevard T9H 4C4
NorsConstruction Equipment Canada ST LP 11301 – 89th Avenue T8V 7M9
Nors Construction Equipment Canada ST LP 6 Burnt Lake Crescent T4S 2L4